This list has been prepared to guide the users of GOLDEN WHEEL heavy duty industrial sewing machines (www.cowboysew.com) and arranged to simplify ordering spare parts, including hooks, bobbin, throat plates, presser feet, feed dogs, folder & binder and other wear and tear parts.
COWBOY #7132 = GOLDEN WHEEL CSL-1801, bottom feed, for ordinary heavy - weight materials
COWBOY #740 = GOLDEN WHEEL CS-6120, walking foot machine for medium weight material
COWBOY #740AU = GOLDEN WHEEL CS-6120BT, walking foot machine with thread trimmer
COWBOY #7132UL = GOLDEN WHEEL CSL-1800, top and bottom feed, for weight materials
COWBOY #7273 = GOLDEN WHEEL CS-273, top and bottom feed for extra heavy materials
COWBOY #74400 = GOLDEN WHEEL CSU-4150, compound feed machine for medium weight material
COWBOY #74400AU = GOLDEN WHEEL CSU-4150BT, compound feed machine with thread trimmer
COWBOY #74420 = GOLDEN WHEEL CSU-4250, two needle, compound feed machine
COWBOY #74420AU = GOLDEN WHEEL CSU-4250BT, 2 needle, compound feed with thread trimmer
COWBOY #7243 = GOLDEN WHEEL CS-243, compound feed, for extra heavy materials
COWBOY #7204 = GOLDEN WHEEL CS-2040, triple feed, for extra heavy materials
COWBOY #7516A = GOLDEN WHEEL CS-2450, cylinder bed zigzag sewing machine
COWBOY #7471 = GOLDEN WHEEL CS-471, top and bottom feed, cylinder bed, extra heavy duty
COWBOY #7341 = GOLDEN WHEEL CS-8242, single needle, cylinder bed, union feed
COWBOY #7341-2 = GOLDEN WHEEL CS-8244L, twin needle, cylinder bed, union feed
COWBOY #7441 = GOLDEN WHEEL CS-441, compound feed, cylinder bed, extra heavy duty
COWBOY #7205 = GOLDEN WHEEL CS-2050, triple feed, cylinder bed, extra heavy duty
COWBOY #7411RL-37= GOLDEN WHEEL CS-411N, long arm transverse seam machine
COWBOY #7461-37 = GOLDEN WHEEL CS-461, long arm cylinder bed, compound feed
COWBOY #7516H = GOLDEN WHEEL CS-2390, post bed bed zigzag sewing machine
COWBOY #9517UL = GOLDEN WHEEL CS-2160, walking foot zigzag sewing machine
COWBOY #9518 = GOLDEN WHEEL CS-2151, 3-step zigzag sewing machine
COWBOY #7204-102 = GOLDEN WHEEL CSL-1810, double needle, moccasin stitch sewing machine
COWBOY #7972= GOLDEN WHEEL CS-6900, shoe patching machine
COWBOY #801= GOLDEN WHEEL CS-747, leather skiving machine
COWBOY #802= GOLDEN WHEEL CS-757, top & bottom feed leather skiving machine
http://www.automatic-sewing.com/industrial-sewing-machine-parts.htm
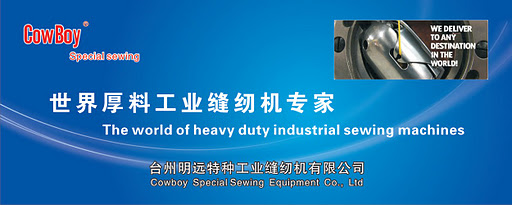
Manufacturer of heavy duty industrial sewing machines for saddles, harness, sail making, lifting slings,safety belts, Big Bag, military parachutes, filters, shoes, upholstered furniture and other sewn products for aerospace, automobile, marine, filtration, environments, outdoor sports, medical, protection, security, buffing wheel etc. Please refer www.cowboysew.com for more information.
Stistics
2012年6月15日星期五
2012年6月4日星期一
How to change the zigzag cam for 9518-30 spinnaker sewing machine
Sailmaster 9518-30 (www.cowboysew.com/product5.htm) is the long arm medium weight zigzag sewing machine for medium weight material.
It sews spinnaker better than any other machine built today.
This machine standard supplied with 4 cams for straight stitch, 1-step zigzag, 2-step zigzag and 3-step zigzag (triple zigzag). During the production, you need to change cams according to different seam requirements. Instructions:I. Change zigzag cam
1.Loosen the hex nut (01), take off the cam(03);
2.Loosen the screw (30), take off the cover (29);
3.Mount the right cam onto the shaft(05) Caution!! The hole on cam must be directed at the dowel pin on the shaft, then light turn the crank (21), make the pin roller (19) on shaft fit to the groove on cam. Mount the wash and hex nut and tighten, then turn the flywheel, the machine should run smoothly.
4.Mount the cover (29) and tighten the screw.
II. Needle timing adjusting Different cam will cause change of timing, please adjust needle timing as following steps:
1. Loosen the screw on top of machine, and take offer top cover.
2. Loosen 4 endless screws(15), turn the upper shaft a bit and then tight 1 of 4 screws (15), turn the flywheel lightly and watch the needle movement, the correct position is: WHEN NEEDLE TIP MOVE TO 8MM ABOVE THE NEEDLE PLATE, THE NEEDLE STOPS SWAY.
3. After finish the adjustment, tighten 4 endless screws (15). Caution! The end face of screw must against the end face of bead flange (12).
4. Mount the top cover and tighten screw.
III. Adjust the gap of worm gear After run for certain time, the gap of worm gear will be appeared, please adjust the gap as flowing steps:
1. Loosen the screw on top of machine, and take offer top cover.
2. Loosen the screw (15) on bead flange (14), move bead flange towards the left;
3.Loosen 4 endless screws(15),slowly move worm gear (16) towards the left, to minimum the gap of worm gear, then tighten screws (15), lightly turn the flywheel, the machine should run smoothly.
4. Move bead flange towards the right and against worn gear.
5. Mount the top cover and tighten screw.
It sews spinnaker better than any other machine built today.
This machine standard supplied with 4 cams for straight stitch, 1-step zigzag, 2-step zigzag and 3-step zigzag (triple zigzag). During the production, you need to change cams according to different seam requirements. Instructions:I. Change zigzag cam
1.Loosen the hex nut (01), take off the cam(03);
2.Loosen the screw (30), take off the cover (29);
3.Mount the right cam onto the shaft(05) Caution!! The hole on cam must be directed at the dowel pin on the shaft, then light turn the crank (21), make the pin roller (19) on shaft fit to the groove on cam. Mount the wash and hex nut and tighten, then turn the flywheel, the machine should run smoothly.
4.Mount the cover (29) and tighten the screw.
II. Needle timing adjusting Different cam will cause change of timing, please adjust needle timing as following steps:
1. Loosen the screw on top of machine, and take offer top cover.
2. Loosen 4 endless screws(15), turn the upper shaft a bit and then tight 1 of 4 screws (15), turn the flywheel lightly and watch the needle movement, the correct position is: WHEN NEEDLE TIP MOVE TO 8MM ABOVE THE NEEDLE PLATE, THE NEEDLE STOPS SWAY.
3. After finish the adjustment, tighten 4 endless screws (15). Caution! The end face of screw must against the end face of bead flange (12).
4. Mount the top cover and tighten screw.
III. Adjust the gap of worm gear After run for certain time, the gap of worm gear will be appeared, please adjust the gap as flowing steps:
1. Loosen the screw on top of machine, and take offer top cover.
2. Loosen the screw (15) on bead flange (14), move bead flange towards the left;
3.Loosen 4 endless screws(15),slowly move worm gear (16) towards the left, to minimum the gap of worm gear, then tighten screws (15), lightly turn the flywheel, the machine should run smoothly.
4. Move bead flange towards the right and against worn gear.
5. Mount the top cover and tighten screw.


Manufacturing Process of Inflatable Boats
Manufacturing Process of Inflatable Boats
www.cowboysew.com/product10.htmInflatable boats have become very popular means of enjoying water sports and recreational boating activities. They are lightweight boats manufactured with their sides and bows made of flexible tubes having pressurized gas within them.
They come in various sizes. In the boats that are longer than 3 meters (10ft), the floor usually consists of 3 to 5 rigid plywood or aluminum sheets fixed between the tubes but not joined rigidly together. Some of the inflatable boats are portable and can be disassembled and packed into a small volume for easy storage. Such a boat, when inflated, is kept rigid crossways by a foldable removable thwart. It makes it appropriate to be used for life saving rafts for larger boats or aircraft, and for travel or recreational purposes. Fabrics Used for Making Inflatable Boats Many raw materials are used in the making of an inflatable boat. It may have rubber floors, either plain or inflatable, that might include steel, wood or aluminum sheets for rigidity. One of the very important raw materials for an inflatable boat is fabrics.
A wide range of inflatable fabric is used for making these boats. For many years all inflatable boats used to be made of Neoprene/Hypalon or rubber materials. The developments in the materials and construction processes have made it possible to make inflatable boats out of strong plastic materials such as PVC too. Today most of the inflatables are made from PVC or Hypalon. Types of Inflatable Boats Inflatable boats are of many types. The most popular ones are rafts and kayaks. Inflatable Rafts: They are simple little platforms for about any type of activity that just requires 'something that floats'. They have several benefits like a 'not so bad' capacity of carrying load, safety given by different air chambers so that the raft doesn't sink along with other features provided by the manufacturers that vary from raft to raft. They are good boats for fishing on rivers and lakes and also work well for floating Class III whitewater sport. Inflatable kayaks: They are heavy duty boats as compared to the rafts.
They are good for long-distance, can carry greater amount of weight and well suited for Class IV whitewater sport. They are good for those who look for long river voyages. These boats can be or cannot be rigid hull or multi hull depending upon the product specification decided by the manufacturers. For the sake of simplicity and knowing the basic process, the manufacturing process of a kayak has been discussed here. The Manufacturing Process A kayak, made of polyethylene fabric, has a body which is a long, hollow shell of uniform thickness. This body is made by a process called rotational molding. The seat and the other components are assembled manually. The shell may be molded in a single piece, or it may be made from two separate pieces that are joined later. Rotational molding requires fairly rounded contours. As a result, the one-piece shells can't have sharp intersections between surfaces. If the design needs to have a sharper intersection, for example, between the hull and the deck, then a two-piece shell is used.
Following process describes the making of a two-piece shell. Thin-walled aluminum molds are used for the hull or the deck. Powdered or granulated polyethylene plastic in measured amounts are mixed with coloring agents and this mixture is loaded into the bottom of the two-piece mold. Hot air welding is the best way to join fabrics, like MASTERBUILT #S700 hot air welding machine (www.cowboysew.com/product10.htm) for inflatable product. A mechanical arm which holds the mold rotates it in two directions at the same time. After the mold is loaded, it is oven heated to 480-840 °F (250-450°C) in the heating station. As the heat from the mold melts the plastic, the mold is slowly rotated in two directions. Gravitational force leads the melted plastic to flow in all the directions into the rotating mold. As a result, it covers the entire surface with a uniformly thick coating of plastic.
Continued heating fuses the melted plastic into a solid layer that attaches itself to the mold. In the cooling chamber, the mold is continually rotated and gradually cooled off with carefully directed sprays of air and then water. The hull or deck further hardens and shrinks away from the mold. Sometimes repeated cycles of heating and cooling are required to make the kayak properly. After the final cooling, it is removed from the mold. The design of the hull and deck are made in such a manner that they fit together at a single seam running horizontally along the length of the boat. Careful sealing is done to ensure that the shell functions as a single structural unit. A decorative strip can also be added to conceal the seam. Sometimes, a keel stiffener is bonded along the length of the shell for additional strength. Closed-cell foam flotation aids are inserted into each end of kayak that are held in place with the help of adhesive. Instead of this, some kayaks use inflatable flotation bags also. These flotation aids aim at keeping the kayak leveled and floating on the surface if, somehow, the craft capsize. If the kayak is designed for bulkheads, then these pieces are bonded in place and sealed with polyurethane sealant. Seat is suspended from straps attached to the sides. Alternatively, it may be supported by a piece of foam bonded to the inside of the bottom of the hull. Adjustable foot brackets or rudder pedals are joined at the inside of the shell, forward of the cockpit, with the help of non-corrosive metal fasteners.
The hatch covers have waterproof gaskets installed before they are put in place and the grab loops are installed. A drain plug is inserted in a molded hole in the shell. The quality control checks are mostly done in the molding process. Proper rotation speed and oven temperature are crucial for producing shells with uniform thickness. To avoid shell warping, utmost care is required during the cooling process. The duration of the heating and cooling cycles, and the intervals between these stages have also to be done in a controlled manner.
How to sew buckles on cargo strap
How to sew buckles on cargo strap
When using tie down straps that have buckles on them you will notice that over time the stitching around the buckles has a tendency to wear out. This happens from all the tugging, pulling and pressure of holding objects in place. Instead of going out and spending money on new straps, learn how to sew the buckles back on the straps. If the buckle happens to break or get lost purchase new ones from your local fabric store. Instructions
1. Trim off any unraveled sections of your tie down straps to remove any wayward threads. Cut the end of the strap to make it perfectly straight (It is better to cut Fabric with a Hot Knife, if you have tool like Cowboy #8901hot knife cuter.
2. Melt the cut end of the strap using a lighter. Hold the flame underneath the end of the strap to melt the threads together. This step is not necessary if you use Cowboy #8901 hot knife cutter (www.cowboysew.com/product8.htm).
3. Read through the directions that came with your buckles as the directions may vary a little from brand to brand.
4. Thread the end on the strap through the buckle. Weave the strap under and over the bar in the buckle.
5. Test the strap to make sure it will tighten when it is pulled. Check to make sure that the buckle is on the right side of the strap so that when you tighten things down the strap will not be twisted.
6. Position the buckle where you want it to stay permanently on the end of the strap. Make sure you have two layers of the strap together where you want to sew the buckle in place.
7. Thread your heavy duty sewing machine like Cowboy #7204 (www.cowboysew.com/product2.htm) with a heavy duty needle, such as is used for sewing through layers of denim or leather, and a heavy duty thread.
8. Sew through the two layers of the strap. Sew slowly and go back and forth over the straps five or six times to make sure it is secure. If you are professional manufacturer of cargo lashing strap, an automated industrial sewing machine like Cowboy #71008 extra heavy duty pattern tacking machine ( www.cowboysew.com/product7.htm) could be taken into consideration, for extra reinforcement.
订阅:
博文 (Atom)